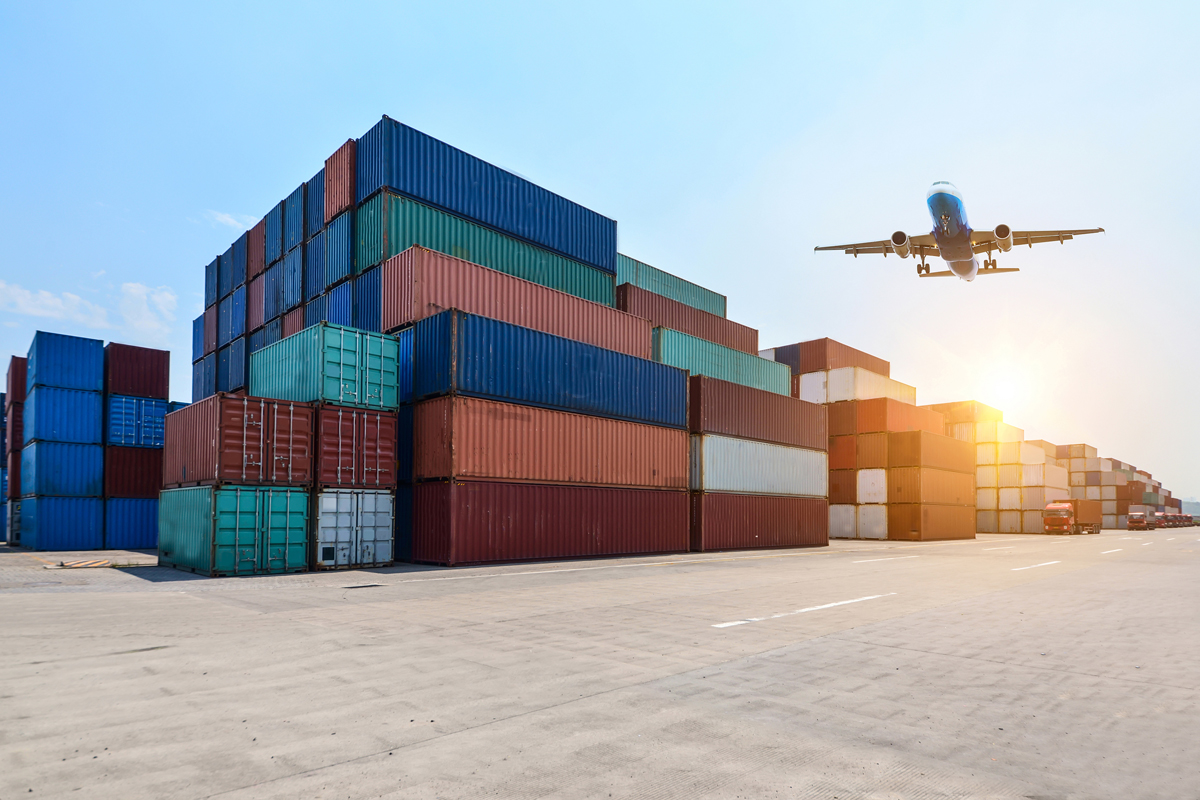
A Well-Run Supply Chain
I can’t believe it’s been more than a year since so many U.S. counties began implementing shelter-in-place rules, and purchasing behaviors drastically changed as families prepared for extended stays in their homes. Many of us will never forget how most stores were cleared of essential items within just a few days, and some as little as a few hours. That created an immediate disruption in every company’s supply chain, including Walmart’s. Businesses with rigid supply chains were in for some big problems, while those that could react quickly to customers’ changing needs were the most successful in responding to the new demand and getting back on track. A flexible supply chain is important at any time, but the effects of COVID-19 on purchasing behavior demonstrated how important.
Typically, a supply chain runs on a 52-week prediction plan based on the previous year’s purchasing patterns coupled with other data like weather and demographic. But unforeseen events like COVID could throw off that 52-week prediction plan, hence the most important thing is that the company remains nimble and flexible in how they operate, and have technology that allows for it. Without that, one can run into trouble.
As a leader of Transportation and Last Mile Technology at Walmart we had to look holistically and identify areas that would help with the changing customer demand and behavior. Below I have listed two areas that had the most impact within Transportation on the success of getting products to Walmart customers: meeting customers’ changing demand and prioritizing safety and speed.
Meet Changing Customer Needs
At Walmart, we made a few smart choices that enabled us to react quickly to our customers’ needs. We looked at the areas within our supply chain that were facing the most pressure and said, what can we do to relieve these pressure points? The first thing that needed attention was our Fulfillment Centers, or FCs. They were facing immense capacity pressure due to the increased volume and were not able to keep up with the backlog. In order to alleviate stress on our FCs, the Transportation team increased our Ship from Store program from 300 to 2000 stores. Since we already built the technology to use 300 of our stores in this way, we were able to increase to 2000 stores very quickly. By utilizing our stores as forward deployed fulfillment nodes to source and ship products, it gave us more fulfillment capacity and helped us to continue to ship essential items and keep the same promise as before.
Then we made changes to two more systems that would help our stores receive and stock the essentials faster to meet the increased customer demand. The first change we made was to quickly implement prioritization capabilities in our appointment scheduling system, which does auto-scheduling of inbound loads (both live and drop loads) that come from suppliers into our distribution centers, or DCs. This prioritization capability enabled us to provide appointments for trailers that were carrying essentials and low-stock items to arrive first.
The second change was specifically for prioritizing drop loads that are already sitting in our yard. To do that, we used our scrappy Trailer Unload Prioritization tool so we could fast-track it during the pandemic, while we work on building this as a core capability in our Yard Management System.. This capability prioritized trailers with essential items to be unloaded first in our DCs. Both changes created intelligent flow for essential items that made it possible to replenish our DCs with the essentials first, which then serves our stores faster, ultimately allowing the customers to get the items they needed most right away.
Safety and Speed
The second most important change we made was to enhance how quickly customers could purchase and receive their products, and making sure it was as safe as possible. Back in March 2020 we were just learning about the virus and how to stay safe, but we knew that limiting person-to-person contact was important. To accommodate this, we knew we had to adjust shopping options to give our customers peace of mind and do our part to ensure their safety as well as the safety of our associates. Practically overnight, Walmart added contactless delivery options.
Due to the massive spike in demand during COVID-19, online grocery slots as far out as 7 days would be booked within minutes, leaving no slots for customers who needed essentials immediately. To alleviate this, we reduced delivery slots availability from 7 days to 2 days at a time and opened capacity on a regular basis. As our capacity improved, we expanded our time slots back to 7 days. This allowed more customers to access online grocery and our contactless pickup and delivery options ensured customer and associate safety.
We also launched Express Delivery so customers could order and receive their products in two hours or less without having to leave their homes. Not only did this technology get products to customers faster, but it also alleviated the pressure on the delivery slot capacity from the early pandemic demand as we added dedicated picking capacity for Express Delivery. This was made possible by again using our stores as forward deployed fulfillment nodes which are closest to our customers.
Our time slots for online grocery have been helping our customers save time by picking up their orders while we do the shopping, with the intention of increasing safety for our most vulnerable customers. We built capabilities to support at-risk groups, enabling specific “At-Risk slots” for the elderly and at-risk populations.
We’ve learned that we can’t just rely on the 52-week outlook. We must be able to see change as it’s happening, and even to anticipate them to prepare for what’s to come. Effectively managing supply chain is a skill we’ll always need because these types of purchase behavior changes aren’t unique to the COVID pandemic. They occur whenever there’s a calamity like hurricanes, earthquakes, or the California wildfires, for example. It’s all about relief points — look for where the pressure is building and make a plan to ease it; have the ability to dynamically reprioritize freight flow to cater to what is needed most by the customers. Technology to support a reliable supply chain must be flexible and nimble in order to respond, and better yet, anticipate.
Simply put, the supply chain is the heart of any company that sells product. It determines the quantity and type of products sold in-store, online, and placed right into our customers hands, and as discussed, how to prioritize to give our customers what they want and need. When the COVID-19 virus began to affect the U.S., we all learned just how important a well-managed supply chain is, not just to the company, but to its customers.
Courtesy : https://medium.com/walmartglobaltech/a-well-run-supply-chain-a-well-run-business-1eb9ea6128e